2019 is dead and the new year is here. Before I put tool to bike in 2020 allow me to reflect on what (if anything) I learned from that first year of wrenching full time. In no particular order or preference here are some of the standout repairs.
Rance is listed first because he was our first customer. He is a busy guy who works two jobs and rides everywhere. The first bike he brought me was a fat bike with two seized mechanical disc brakes, a freewheel that couldn’t be removed and a rear wheel with ½” of play in the hub. I made his bike work and didn’t charge him a ton of money. He has since moved from the neighborhood but he still brings in his bikes and recommends me to others.
Julie is our neighbor next door. She brought in her bike for a tune-up, two tires, a bike computer, a light and a lock. As I did the work her tab was adding up and I was worried she would have sticker shock. Nope. Supporting a local business is what she wanted to do, and she insisted on paying full price for the tune-up (we had been running a Grand Opening special). I put a lot of effort into making a bike work right and when it leaves my only hope is that it gets ridden. This fall, after our first newsletter was published, Julie stopped back in to see how our business was doing and report back on how much fun she was having riding her bike.
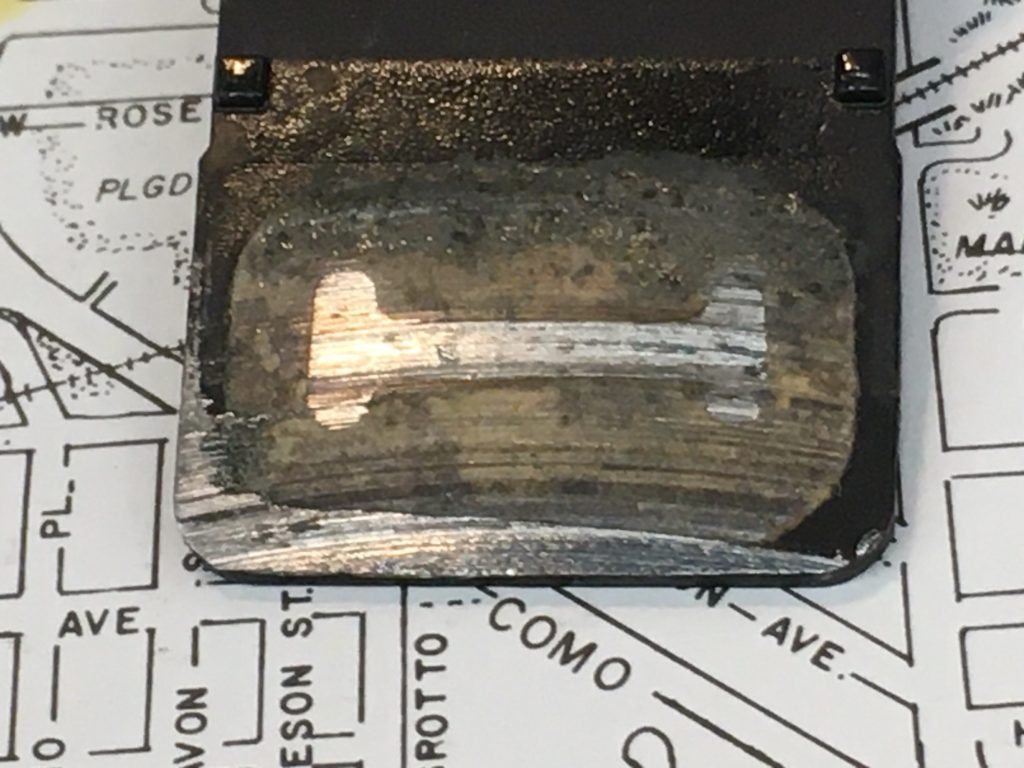
Please apologize to your rotor.
Jonathan rides more real and virtual miles than anyone I know. Because I like working on bikes that get ridden, he is a great customer to have. His Felt was cursed with a crappy rear hub and he commissioned a wheel build. The twist: he wanted me to reuse the rim (so it matched the front). Building a wheel changes the rim in radial and lateral true and because of that reusing a rim for a new build is usually inadvisable. (Never ever reuse spokes and nipples.) But it all worked out and he’s happy. Jonathan also has the distinction of the most worn brake pads I’ve ever seen.
Mark is a recent transplant to the neighborhood. He had a mid 1980s Miyata that had been parked for awhile. The bike had a lot of good memories and he wanted to make some new ones. We embarked on a custom build that brought the bike into the 21st century with integrated shifting, an external bearing bottom bracket, wide cross section rims and baller Continental GP 5000 tires. He stopped by this fall to thank us for being here, and we thanked him for getting involved in bike advocacy.
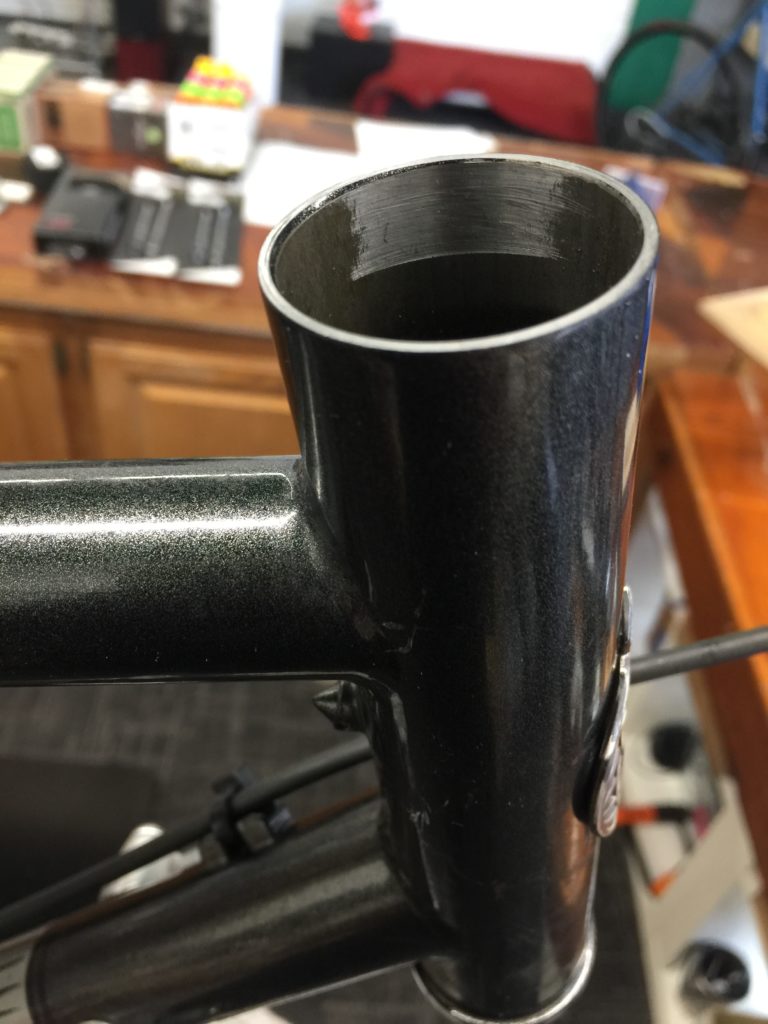
The headtube post facing and reaming. The bare metal shows where tube was ovalized.
Bob had a (sweet!) 2012 Salsa Vaya and he wanted to lighten the bike and improve its braking. His challenge was finding an affordable carbon disc fork for a 1 ⅛” steerer. I happened to have one. Simple fork and headset swap, right? Wrong. (Pro tip: don’t ride with a loose headset. If you can turn those spacers under your stem or if you feel a clunk from the front end, get that headset adjusted. The alternative may be an ovalized headtube.) I got Bob squared away and it was a win for me because sooner or later I had to use those expensive cutting tools.
Juan. I forget what bikes he owns. We just talk politics, urban planning, and religion. I do remember one bike he doesn’t own: a kid riding home from his shift at McDonald’s hit the curb next to Juan’s house and did a superman onto the lawn. While the rider recovered in the hospital Juan brought his bike to me for fixing. Later he brought us a squash that he grew.
Tyler owns a gorgeous purple 2017 Salsa Fargo that had bad shifting and way too much tire. The former owner had stuffed a 29” x 3.0” tire into a frame meant for something smaller. The remedy was a new wheelset with a narrower rim and 2.6” tire — which I happily built. Shrinking the tire allowed the rear wheel to be moved forward in the frame which, in turn, solved the shifting problem that had been vexing me. Tyler had exquisite taste in bikes and beer.
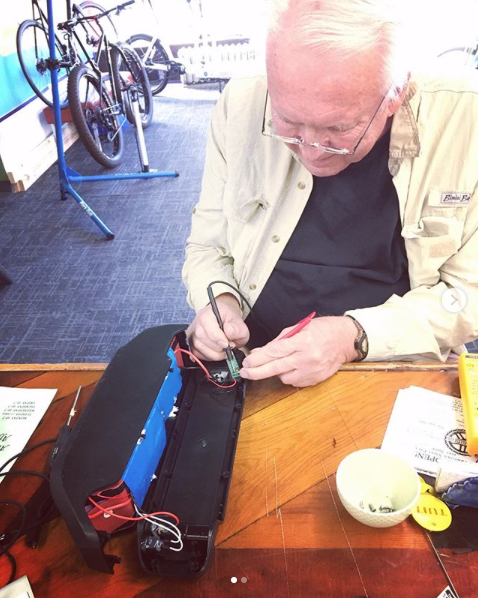
My old man soldering a battery connector.
E-bike conversion trifecta: an Amazon-sourced trike, a recumbent, and a Cannondale Cujo were all given the gift of electricity. I didn’t hate working on one of these bikes — can you guess which? I can joke about them now but at the time I wasn’t laughing. Findings: 1) it is possible to electrify a trike on a budget; 2) a 750w motor generates A LOT of torque and it will shred a standard fork’s dropouts; 3) the only thing more frightening than riding a 2 wheel recumbent in traffic is doing it with a 750w motor slung on the front; 4) Bafang makes a damn fine mid-drive retrofit and has excellent customer service; and 5) no one knows shit about repairing these e-systems… except for my old man (see above photo). To our e-bike pioneers: I salute you guys and thank you for the opportunity to gain this knowledge.
Matt rides everywhere, all the time. He has a Trek fat bike and a Bamboo fixed gear. His bikes needed a lot of work. These are the service notes from one:
Pedals bearings/bushing were exhausted (replace pedals); chain and cassette were worn and not shifting properly (replaced both and installed new derailleur cable and 5mm housing); ultrasonic cleaning of derailleur and crank; rear brake pads were exhausted (replaced and cleaned rotor); rear caliper and rotor were misaligned (reset caliper pistons, cleaned mount/adaptor hardware, flushed caliper body with steam); removed and resurfaced front brakes pads; cleaned front rotor and realigned rotor and caliper; checked headset preload and stem bolt torque; cleaned frame/fork/wheels; adjusted rear derailleur; and inflated tires to ~ 20 psi.
Matt picked up his bikes and a few days later he chased down and tackled a bike thief to get one of them back. Matt brought the bike back to us to make it right. With a new derailleur hanger he was back in business. Have many happy miles, man, and see you next year.
Nick happened by on one of those days in late fall which was a gift — 70 degrees and sunny. He had with him a beautiful black Lemond Washoe with Dura Ace Di2 (9020). I charged the battery, updated the firmware, adjusted the derailleurs, and inflated the tires. Turns out that at one point he even worked with Lemond. This interaction checked all the boxes: Di2 bike (nice to have some variety after all those Diamondbacks), cool customer, and Lemond — hero — content.
Tall Nick came into our shop one day with a fixed gear that looked like he made it himself (he did). I de-tensioned and rebuilt both wheels on that bike. That was a time-consuming but simple task compared to pressing a Cane Creek EC40 into that frame. It was the hardest metal I have ever cut and then there’s the truly terrifying thing: removing metal from a handbuilt frame. Yeah, no backsies on that.
Catherine had a late 90s Bianchi road bike and she wanted a more comfortable riding position. Rather than steering her towards a new bike we kept her beautiful Bianchi on the road by swapping her drop bars for straight bars and her STI levers for thumb shifters and brake levers. Because her drivetrain was 2×7 sourcing shifters that would work with her derailleurs was tricky — the selection was limited, many were out of stock, and I was working within a budget. The solution was to use a triple shifter with cable slack to get the correct about of pull.
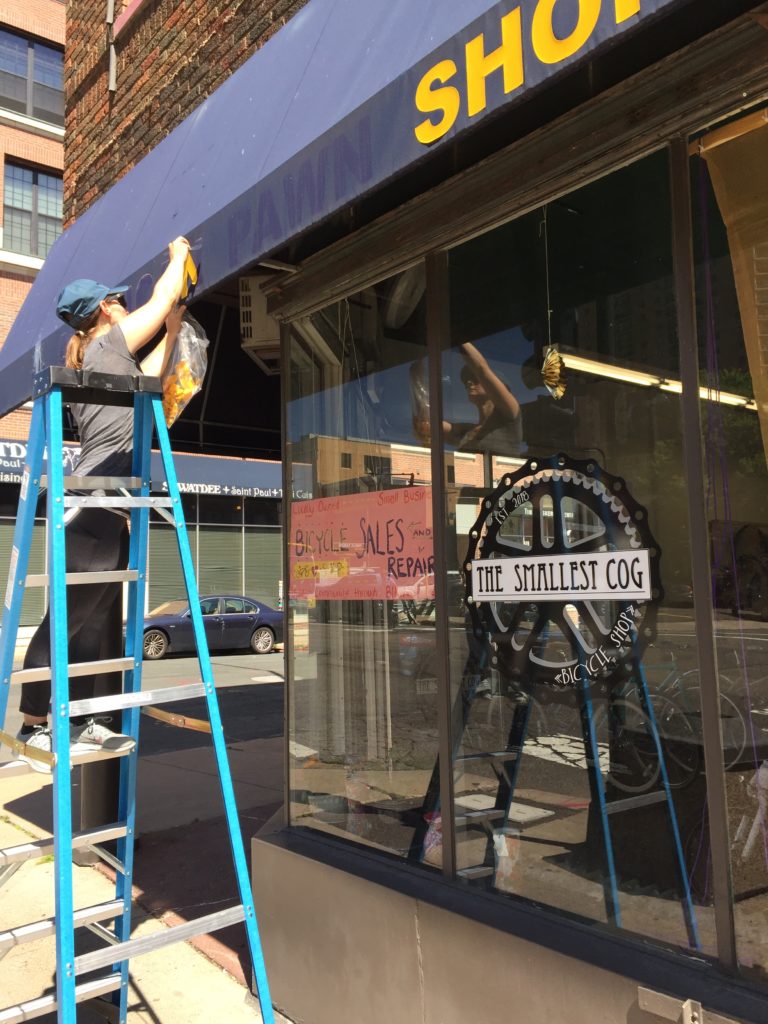
My personal favorite repair: removing the pawn shop lettering from our awning.
Ryan’s custom asymmetrical wheels. When I lived in DC I was the go-to wheelbuilder for my friends. In 2019 one of them purchased a Guerilla Gravity (made in Colorado) and he commissioned a wheelset that used White Industries CLD+ Boost hubs and Stan’s Flow 29+ rims. It was 32 hole, silver spokes, brass nipples and 3-cross for both wheels. Here’s the catch: the frame was asymmetrical with a 3mm offset to the driveside.
I scratched my head about this for a week before I figured out how to build it. Build it just like a regular wheel until the spokes hit 90% tension. Then back off the truing stand feeler gauges until they are 3 mm from the rim. Finally, tighten the non driveside spokes until the rim contacts the left feeler gauge.
Making sure that any wheel is true and dished requires a calibrated truing stand and constant checking with the dishing gauge (never trust just one instrument… Boeing 737 Max). The final verification is seeing how the wheel sits in the frame. Is it too close to one of the chainstay? So it is always good to have the frame on hand when building a wheel and that is especially true when building something unusual as was the case here. But the frame was in Virginia so I was building blind. Gulp.
I packed up the wheels and shipped them to Ryan. The moment of truth happened about a week later when he dropped the wheels into the frame. They were dished perfectly. Heart attack averted and wheelbuilding hubris still in tact.
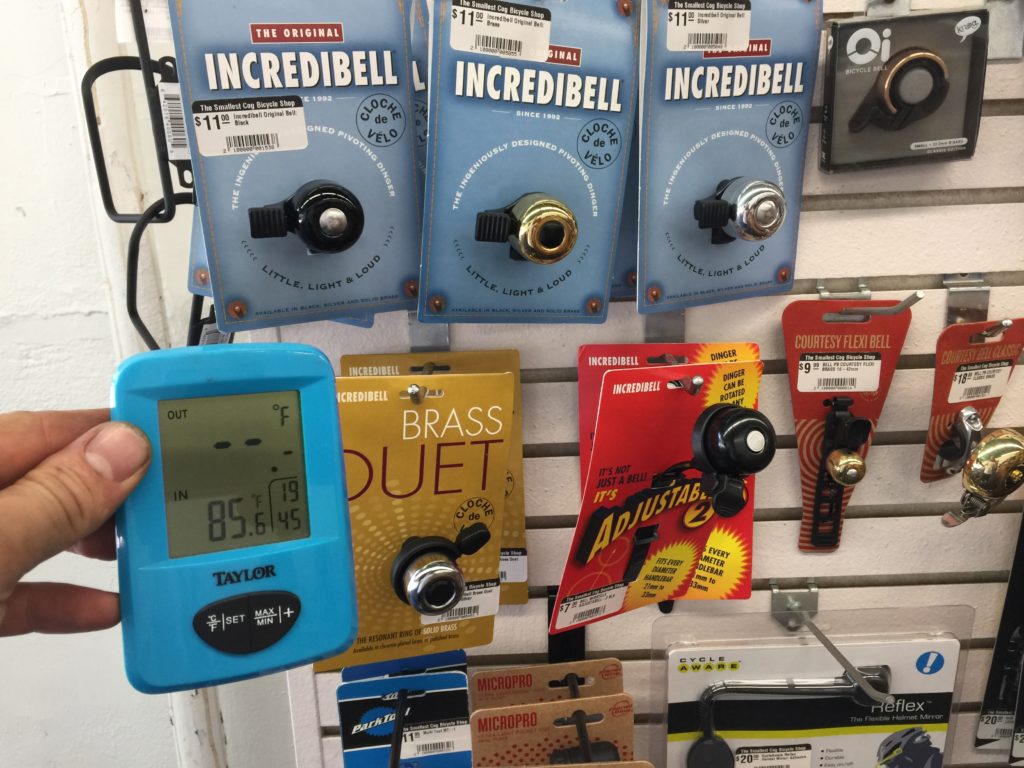
The one repair we won’t be making is adding air conditioning. Because people would never leave!
Least Favorite Repairs
CenturyLink. When their contractors busted up our street to lay some cable. It was three days of jackhammering and lost business. They did fix our curb ramp (because I asked). I had my fill of watching people in wheelchairs nearly tip over due to the pothole.
Trek Road Bikes. This is going to seem petty but… the proper technique for wrapping drop bars is to start at the end and work your way towards the stem. Trek didn’t do this; they started at the stem and worked their way to the bar ends. What that means is that every time I have to replace a shift and/or brake cable and housing on a Trek with Shimano 5700/6700/7900 or newer I had to fully unwrap the bar tape. In addition to the 15-20 minutes this adds to a repair, the result never quite looks right because the bar tape has worn down and changed shape. SMH.
Honorable mention: Anything French.